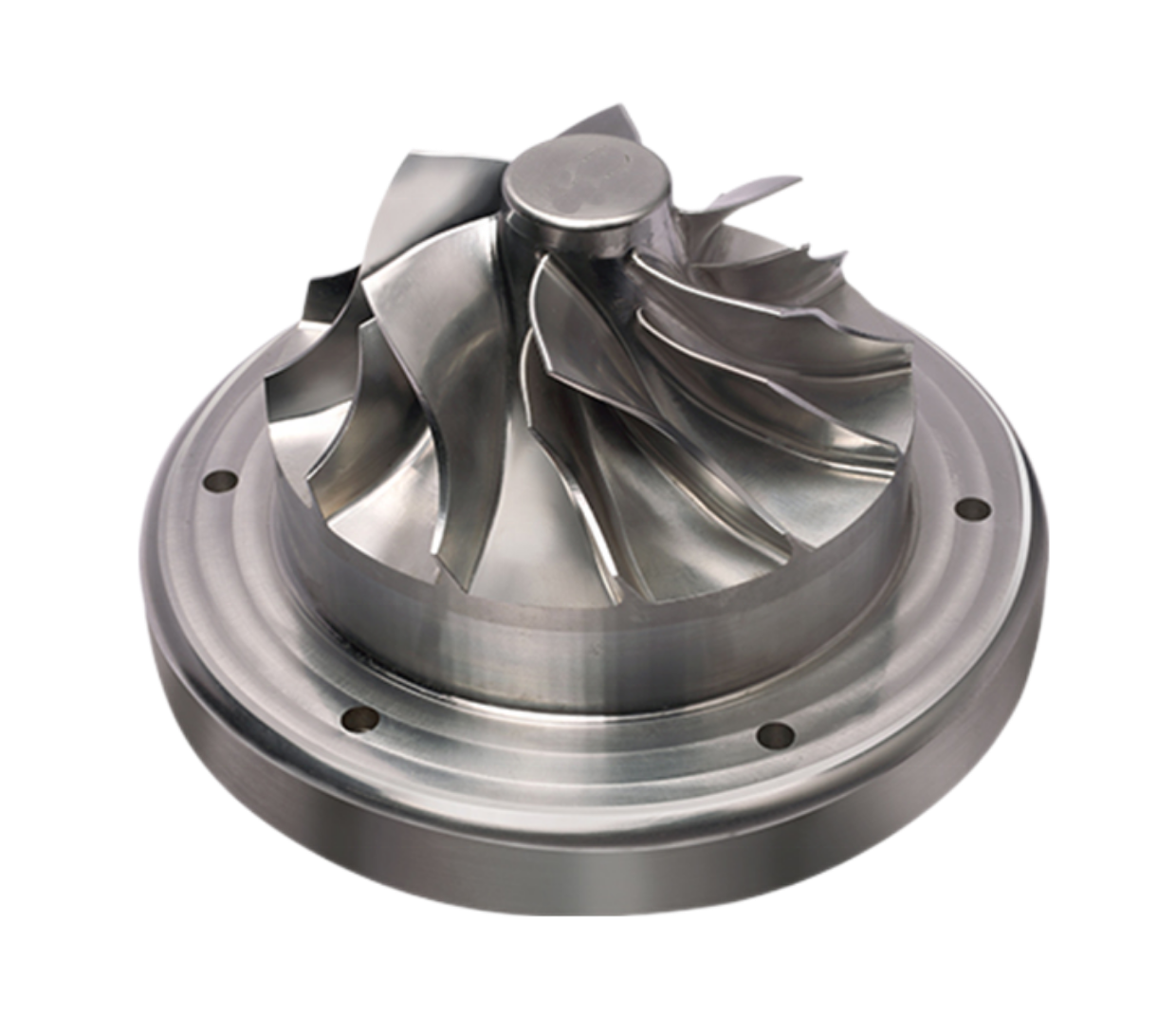
Design Tips of CNC Milling
Here are some design tips for CNC milling: choose appropriate tooling, optimize cutting parameters, consider material properties, and design for manufacturability.
> 3-Day Lightning Delivery
> North America’s Top 10 One-stop Solutions
> 75+ Choices of Materials
10 Design Tips of CNC Milling
CNC milling is a versatile and precise manufacturing process that can produce complex parts with high accuracy. To ensure the best possible results, it’s important to design parts with the CNC milling process in mind. Here are some tips to help you design parts for CNC milling:
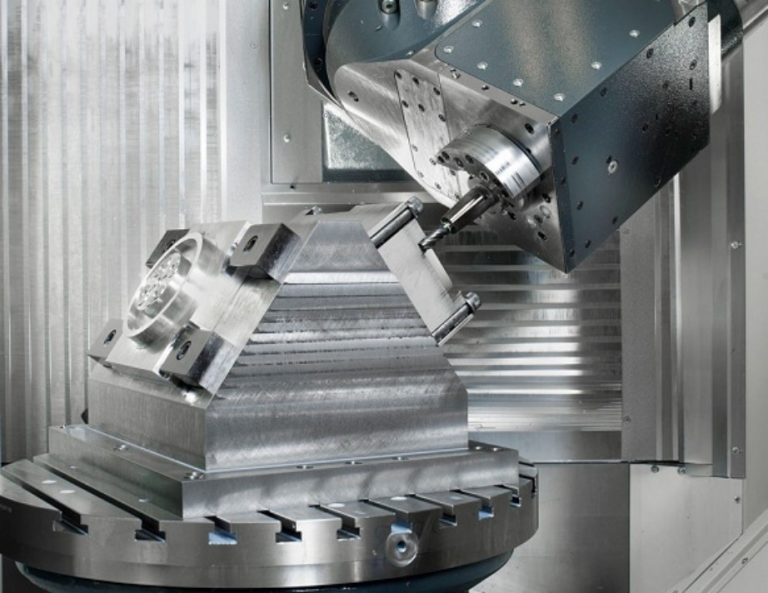
Tip 1: Consider the part’s orientation
When designing a part for CNC milling, it’s important to consider how the part will be oriented during the milling process. Orienting the part in the correct position can help to minimize the amount of material that needs to be removed, reduce the number of setups required, and ensure that the part is machined with the highest possible accuracy.
Tip 2: Minimize the number of setups
Each setup required for machining a part adds time and cost to the manufacturing process. To minimize the number of setups required, design parts that can be machined from a single orientation, use standard tooling, and avoid features that require specialized tooling or fixtures.
Tip 3: Design with the end mill in mind
End mills are the cutting tools used in CNC milling. To ensure the best possible results, design parts with the end mill in mind. This means avoiding features that are too small or too deep for the end mill to reach, designing features with the right radius to match the end mill, and selecting the right end mill for the job.
Tip 4: Choose the right materials
CNC milling can be used to machine a wide variety of materials, including metals, plastics, and composites. When selecting materials for CNC milling, consider factors such as material strength, machinability, and cost.
Tip 5: Avoid complex shapes
Complex shapes can be difficult to machine with CNC milling, which can lead to longer machining times and higher costs. To minimize these issues, avoid complex shapes and features that require multiple setups or specialized tooling.
Tip 6: Use fillets and chamfers
Fillets and chamfers can help to reduce stress on the cutting tool and increase the overall tool life. By adding fillets and chamfers to your design, you can help to ensure that the part is machined with the highest possible accuracy and minimize the risk of tool failure.
Tip 7: Optimize tool paths
The tool paths used in CNC milling can have a significant impact on the quality of the finished part. To ensure the best possible results, optimize the tool paths to minimize tool changes, reduce machining time, and ensure that the part is machined with the highest possible accuracy.
Tip 8: Consider the tolerances
When designing parts for CNC milling, it’s important to consider the tolerances required for the intended application. Design parts with tight tolerances only if they are necessary for the intended application, as tighter tolerances can lead to longer machining times and higher costs.
Tip 9: Use simulations
Computer simulations can be used to validate the design and predict potential machining problems, such as tool deflection or cutting forces. By using simulations, you can optimize the design and tool paths before the part is machined, which can help to minimize the risk of errors and reduce machining time.
Tip 10: Test the design
Before machining the final part, it’s a good idea to test the design by machining a prototype or using a 3D printing service to create a test part. Testing the design can help to identify potential issues and ensure that the part is machined with the highest possible accuracy.
Looking for CNC Milling Services On-demand?
Are you in need of high-quality CNC Milling services on-demand? Look no further than Naxtry! Our experienced team and state-of-the-art equipment ensure precise and efficient manufacturing of your parts or products. Contact us today for a quote!