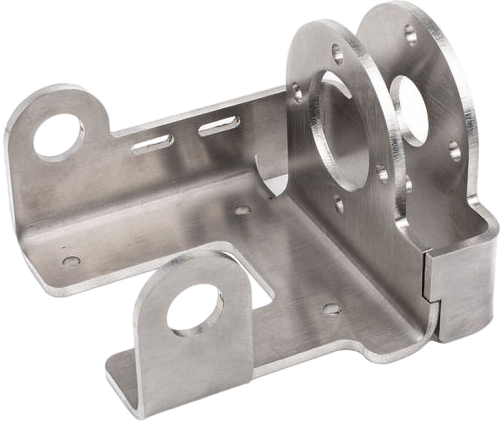
Design Tips of Sheet Metal Bending
When designing for sheet metal bending, ensure proper bend radius, use appropriate tooling, and consider material thickness and grain direction for optimal results.
> 3-Day Lightning Delivery
> North America’s Top 10 One-stop Solutions
> 75+ Choices of Materials
Design Tips of Sheet Metal Bending
Sheet metal bending is a common manufacturing process used to shape metal sheets into various forms. It involves deforming the material by bending it at a particular angle. Here are six design tips to keep in mind when creating sheet metal parts to ensure successful bending:
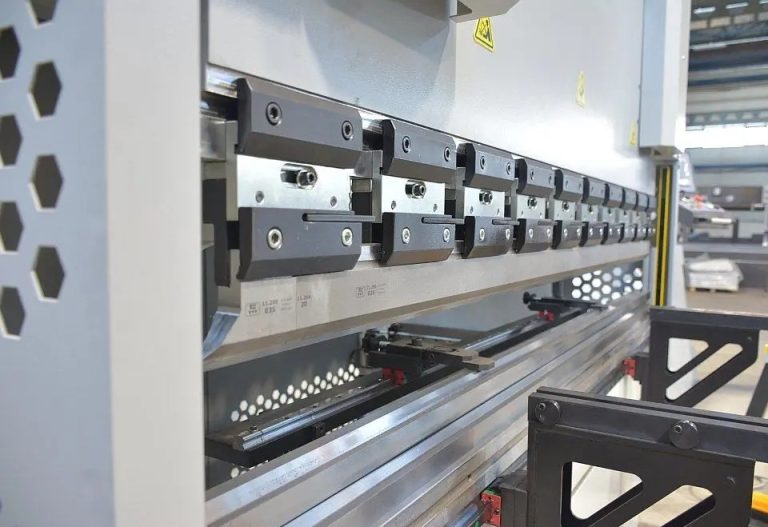
Tip 1: Material Selection
Material selection plays a critical role in sheet metal bending. The type of material used determines the bending radius and the maximum angle that can be achieved without cracking or rupturing. Consider the sheet metal’s thickness and properties, including its ductility and tensile strength. Soft materials, such as aluminum and brass, are easier to bend than harder materials like steel. Stainless steel is more challenging to bend than regular steel due to its higher strength.
Tip 2: Bend Radius
The bend radius determines the minimum size of the bend that can be achieved. A smaller bend radius results in a tighter bend angle, but it also increases the risk of cracking or rupturing the material. It’s important to select a bend radius that is appropriate for the material and the desired bend angle. Generally, the bend radius should be at least equal to the sheet metal’s thickness.
Tip 3: Bending Direction
The bending direction determines the orientation of the bend relative to the material’s grain direction. Bending across the grain results in less spring-back and more accurate bending, whereas bending along the grain can result in more spring-back and less accuracy. The direction of bending should be considered when designing sheet metal parts to ensure proper grain orientation.
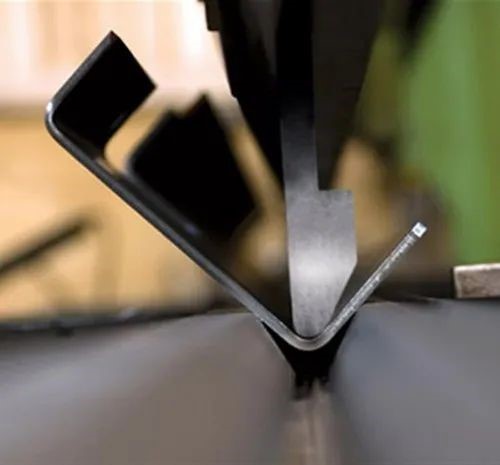
Tip 4: Avoid Sharp Corners
Sharp corners are more challenging to bend than rounded corners. When designing sheet metal parts, avoid sharp corners and opt for rounded corners instead. The radius of the corners should be at least equal to the sheet metal’s thickness. This will help prevent cracking or rupturing of the material during the bending process.
Tip 5: Bend Relief
Bend relief is an indentation or cutout that is placed near the bend line. It allows the material to deform more easily during the bending process, resulting in more accurate and consistent bends. Adding bend relief can also help prevent material distortion and cracking, particularly in thicker materials. The size and placement of the bend relief should be carefully considered when designing sheet metal parts.
Tip 6: Proper Tooling
The tooling used to bend the sheet metal is critical in achieving accurate and consistent bends. The tooling must match the material’s thickness and properties, including its ductility and tensile strength. Using the wrong tooling can result in uneven bending, cracking, and rupturing of the material. It’s essential to select the appropriate tooling for the specific sheet metal part being manufactured.