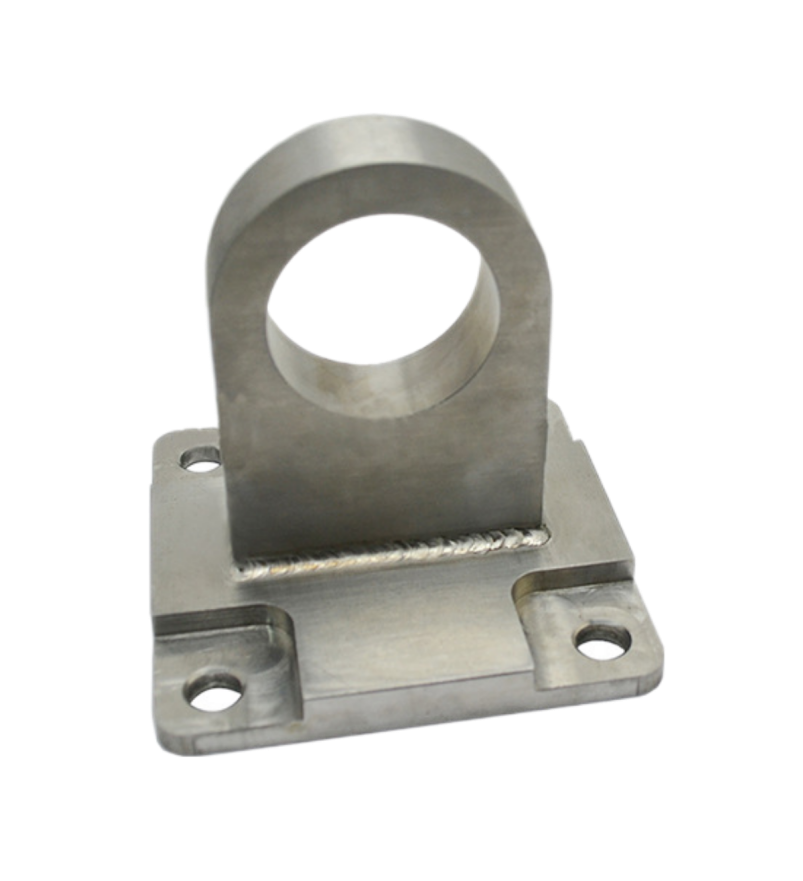
Design Tips of Welding
Some design tips for welding include selecting the appropriate welding method for the material, ensuring proper joint preparation, and selecting suitable welding equipment and parameters.
> 3-Day Lightning Delivery
> North America’s Top 10 One-stop Solutions
> 75+ Choices of Materials
Design Tips of Welding
Welding is an important manufacturing process used to join two or more pieces of metal or thermoplastics together.Designing parts for welding requires careful consideration to ensure strong and reliable joints. Here are some design tips to help you create weld-friendly parts:
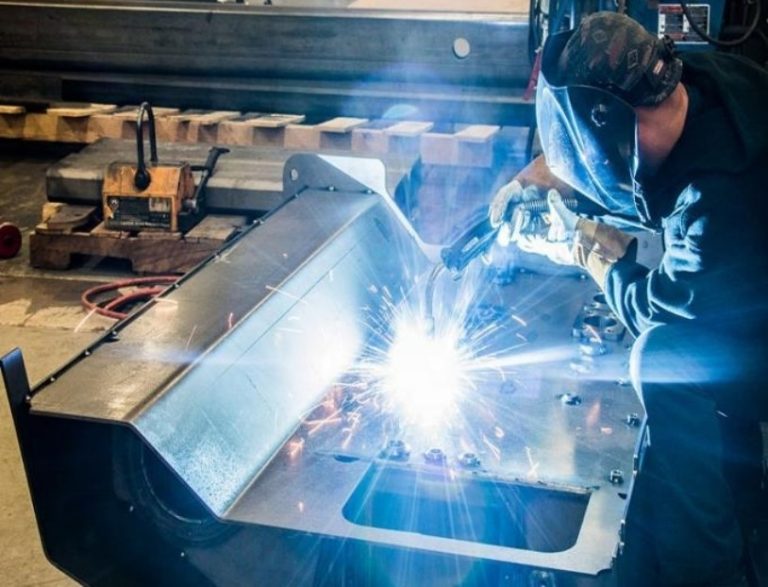
Tip 1: Joint Design
l Choose appropriate joint types based on the application and loading conditions, such as butt joints, lap joints, or T-joints.
Ensure sufficient joint area and overlap for a strong bond and effective load transfer.
l Avoid complex joint configurations that can hinder welding accessibility and quality.
Tip 2: Material Selection
Select materials that are compatible for welding and have similar composition and mechanical properties.
Consider the weldability of the chosen materials, including their susceptibility to cracking, distortion, or other welding defects.
Tip 3: Joint Preparation
Provide proper joint preparation, including edge beveling, chamfering, or grooving, to ensure good penetration and fusion during welding.
Remove any surface contaminants, such as oil, rust, or paint, that can negatively impact the welding process and weld quality.
Tip 4: Welding Processes and Techniques
l Choose the appropriate welding process, such as MIG (Metal Inert Gas), TIG (Tungsten Inert Gas), or arc welding, based on the material, joint type, and application requirements.
l Select welding techniques, including the use of filler material, welding speed, and heat input, to achieve strong and aesthetically pleasing welds.
Tip 5: Weld Access and Clearance:
l Ensure sufficient access for the welding torch or electrode to reach the joint, especially in complex or confined areas.
l Provide adequate clearance between parts to accommodate the welding process, electrode movement, and heat dissipation.
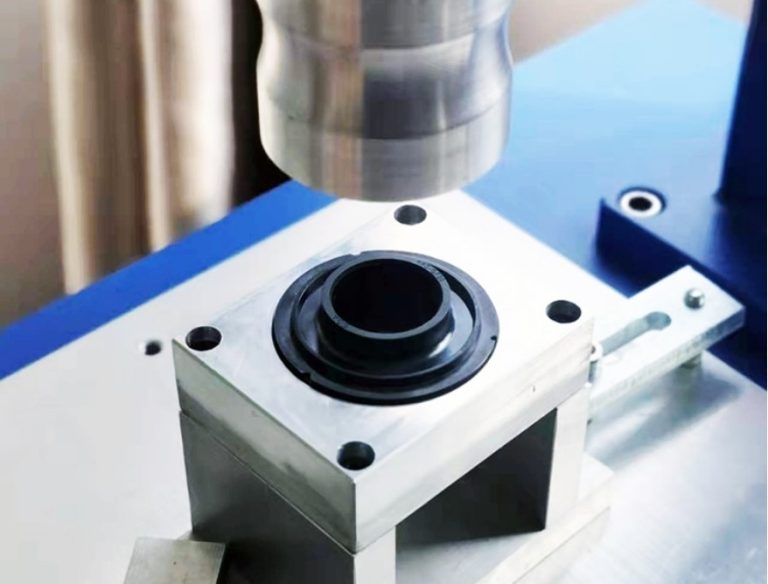
Tip 6: Welding Symbols and Specifications
l Utilize welding symbols, as per industry standards (e.g., AWS, ISO), to communicate the desired weld type, size, and other specifications.
l Clearly define welding requirements, such as weld size, penetration depth, and allowable tolerances, in your design documentation.
Tip 7: Fillet Welds
l Design fillet welds with appropriate leg lengths and throat thicknesses to ensure sufficient strength and prevent excessive material buildup.
l Avoid excessive reinforcement or undercutting, which can weaken the weld or cause stress concentrations.
Tip 8: Avoid Distortion and Residual Stresses:
l Minimize distortion and residual stresses by carefully planning the welding sequence, using tack welds to secure parts in position, and employing proper fixturing or clamping techniques.
l Consider post-welding treatments, such as stress relieving or heat treatment, to alleviate residual stresses and enhance the part’s dimensional stability.
Tip 9: Quality Control and Inspection:
l Incorporate inspection features, such as access holes or inspection ports, to facilitate non-destructive testing (NDT) and weld quality assessment.
l Implement quality control measures, including visual inspection, ultrasonic testing, or radiographic examination, to verify the integrity of the welded joints.
Tip 10: Collaboration with Welding Experts:
l Consult with experienced welding professionals or welding engineers to ensure the design meets welding standards, best practices, and specific project requirements.
l Seek their advice on material selection, joint design, welding techniques, and any other considerations that can enhance weld quality and structural integrity.