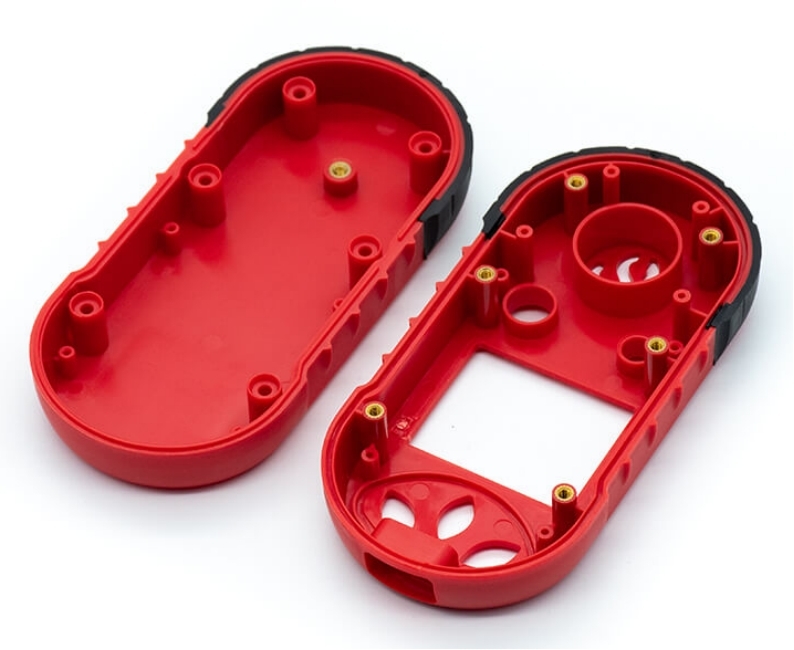
Optimizing Injection Molding Efficiency: Tips for Cost-effective Production
Share tips and strategies to optimize injection molding processes for maximum efficiency and cost-effectiveness.
> 3-Day Lightning Delivery
> North America’s Top 10 One-stop Solutions
> 75+ Choices of Materials
Injection molding is a widely used manufacturing process known for its versatility and efficiency. To remain competitive in today’s fast-paced market, it is essential to optimize injection molding processes for maximum efficiency and cost-effectiveness. In this blog, we will explore valuable tips and strategies to help manufacturers streamline their production, minimize waste, and optimize resource utilization. By implementing these optimization techniques, businesses can enhance their operational efficiency, reduce production costs, and ultimately achieve greater profitability.
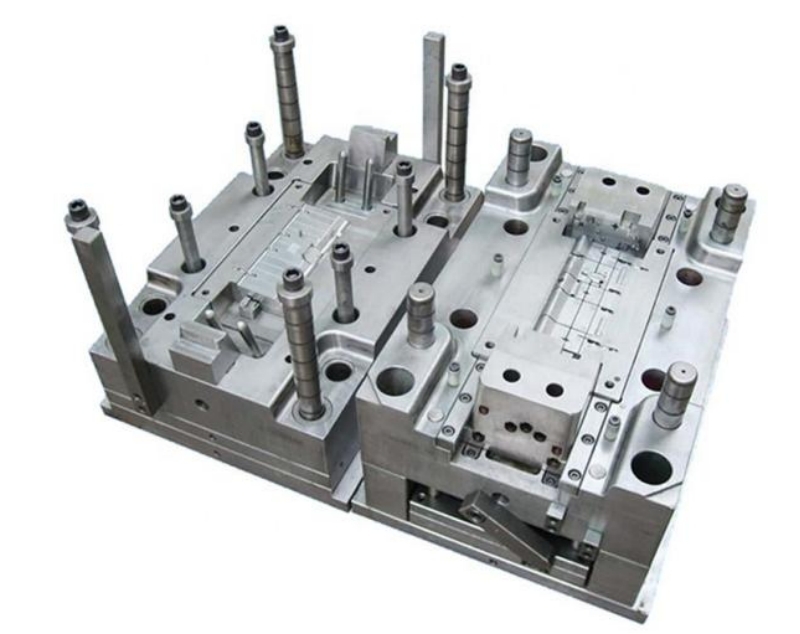
1.Design for Manufacturability :
The key to cost-effective injection molding starts with design for manufacturability (DFM). We will discuss the importance of designing parts with the manufacturing process in mind, considering factors such as wall thickness, draft angles, part consolidation, and gating design. By optimizing part designs for easy moldability and minimizing the need for Post-Processing, manufacturers can significantly reduce production costs and cycle times.
2.Material Selection and Optimization :
Selecting the right material is crucial for achieving cost-effective injection molding. We will explore different material options and their characteristics, including factors such as strength, durability, temperature resistance, and cost. Additionally, we will discuss material optimization techniques such as lightweighting and material substitution, which can help reduce material usage and lower production costs without compromising part performance.
3.Process Optimization and Automation:
Optimizing the injection molding process is key to achieving maximum efficiency and cost-effectiveness. We will discuss process optimization techniques such as setting appropriate injection parameters, optimizing cooling times, and minimizing cycle times. Additionally, we will explore the benefits of automation in injection molding, including robotics and automated systems for part handling, mold changeovers, and quality control. Automation can significantly improve production efficiency, reduce labor costs, and enhance product consistency.
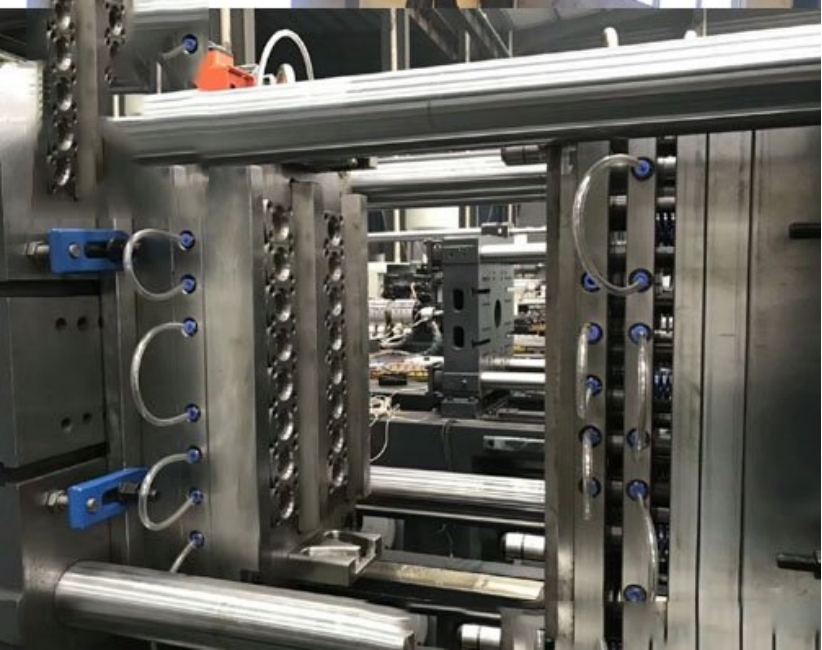
4.Tooling Optimization and Maintenance :
Well-maintained and optimized molds are essential for cost-effective injection molding. We will discuss the importance of proper mold design, including considerations such as gate placement, venting, and ejection mechanisms. Regular mold maintenance, including cleaning, lubrication, and inspection, will also be highlighted. Proper tooling maintenance not only prolongs the lifespan of molds but also ensures consistent part quality, reduces downtime, and minimizes the risk of costly mold repairs.
5.Waste Reduction and Recycling :
Minimizing waste is crucial for cost-effective injection molding and environmental sustainability. We will explore strategies for waste reduction, including optimizing runner systems, regrinding scrap materials, and implementing closed-loop recycling systems. By efficiently managing material waste and incorporating recycling initiatives, manufacturers can reduce material costs and contribute to a more sustainable manufacturing process.
6.Continuous Process Monitoring and Quality Control :
Implementing robust process monitoring and quality control measures is vital for cost-effective injection molding. We will discuss the importance of real-time process monitoring through sensors and data analytics, allowing manufacturers to detect and address potential issues before they escalate. Additionally, we will explore quality control techniques such as statistical process control (SPC) and automated inspection systems to ensure consistent part quality and minimize the risk of defective products.
Optimizing injection molding efficiency is essential for cost-effective production. By following the tips and strategies outlined in this blog, manufacturers can streamline their processes, minimize waste, and achieve greater profitability. From design for manufacturability and material optimization to process automation, tooling optimization, waste reduction, and quality control, every aspect of the injection molding process plays a significant role in driving efficiency and cost-effectiveness. By continuously evaluating and improving their production practices, manufacturers can stay ahead of the competition, meet customer expectations, and thrive in the dynamic world of injection molding.