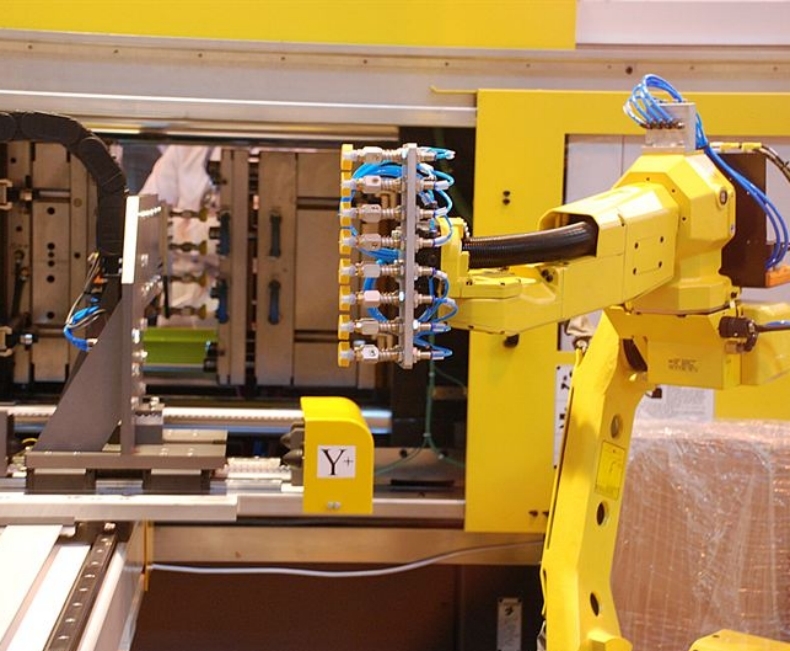
The Future of Injection Molding: Industry Trends and Innovations
Explore the latest trends and innovations shaping the future of injection molding.Provide insights into how these advancements are revolutionizing the injection molding industry.
> 3-Day Lightning Delivery
> North America’s Top 10 One-stop Solutions
> 75+ Choices of Materials
Injection molding has long been a crucial manufacturing process, and as technology continues to advance, the future of this industry holds exciting possibilities. In this blog, we will explore the emerging trends and innovations that are shaping the future of injection molding. From advancements in materials and machinery to the integration of automation and digital technologies, we will delve into the key factors driving the evolution of injection molding. By understanding these trends, manufacturers can stay ahead of the curve and unlock new opportunities for efficiency, productivity, and product innovation.
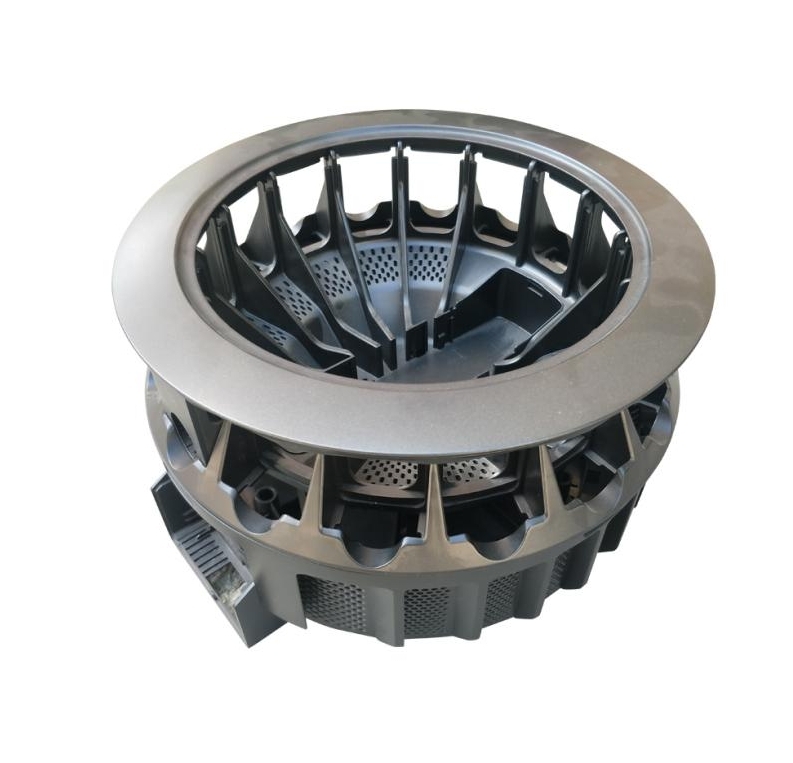
1.Advanced Materials for Enhanced Performance :
One of the key trends in injection molding is the development of advanced materials that offer improved performance characteristics. We will discuss the emergence of high-performance polymers, composites, and bio-based materials that provide enhanced strength, durability, heat resistance, and environmental sustainability. These materials open up new possibilities for applications in industries such as aerospace, automotive, medical, and electronics. We will also explore the importance of material selection and the role of material suppliers in driving innovation in injection molding.
2.Automation and Robotics for Increased Efficiency:
Automation and robotics are transforming the injection molding landscape, enabling manufacturers to achieve higher levels of efficiency and productivity. We will discuss the integration of automated systems, such as robotic arms and machine tending solutions, in the injection molding process. These technologies streamline operations, reduce cycle times, minimize errors, and increase throughput. Additionally, we will explore the concept of lights-out manufacturing, where injection molding machines can operate autonomously with minimal human intervention, further enhancing productivity and cost-effectiveness.
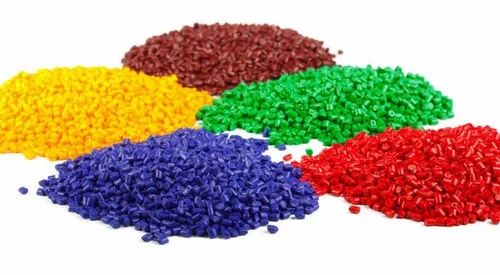
3.Digitalization and Industry 4.0 Integration :
The injection molding industry is embracing digitalization and the principles of Industry 4.0, leading to improved connectivity, data-driven decision-making, and smart manufacturing. We will discuss the integration of sensors and IoT devices in injection molding machines, enabling real-time monitoring and predictive maintenance. Furthermore, we will explore the use of data analytics and artificial intelligence (AI) to optimize process parameters, improve product quality, and reduce material waste. The adoption of digital twins, virtual simulations, and digital workflow management systems will also be highlighted, showcasing the benefits of a digitally connected injection molding ecosystem.
4.Sustainability and Circular Economy:
In an increasingly environmentally conscious world, sustainability and the circular economy are gaining prominence in injection molding. We will explore the growing demand for eco-friendly materials, recycling initiatives, and waste reduction strategies. Manufacturers are focusing on closed-loop systems, where plastic waste is recycled and reintroduced into the production process, minimizing environmental impact. Additionally, we will discuss the importance of designing for sustainability, including lightweighting, part consolidation, and the use of bio-based or recycled materials to create more environmentally friendly products.
5.Customization and Agile Manufacturing :
The future of injection molding lies in the ability to meet the growing demand for customization and agile manufacturing. We will explore the advancements in multi-material injection molding, allowing for the production of complex, multi-component parts in a single operation. The integration of 3D printing technologies with injection molding offers the potential for rapid prototyping, tooling optimization, and on-demand production. By embracing these trends, manufacturers can address evolving customer needs and deliver highly customized products with shorter lead times.
The future of injection molding is driven by advancements in materials, automation, digitalization, sustainability, and customization. As manufacturers embrace these trends, they can unlock new levels of efficiency, productivity, and product innovation. The integration of advanced materials enhances performance and expands the application possibilities of injection molding. Automation and robotics improve efficiency and reduce cycle times, while digitalization and Industry 4.0 integration enable data-driven decision-making and smart manufacturing. Sustainability and circular economy practices contribute to a greener future. Lastly, customization and agile manufacturing cater to evolving customer demands. By staying at the forefront of these industry trends and embracing innovation, manufacturers can secure a competitive advantage and thrive in the future of injection molding.