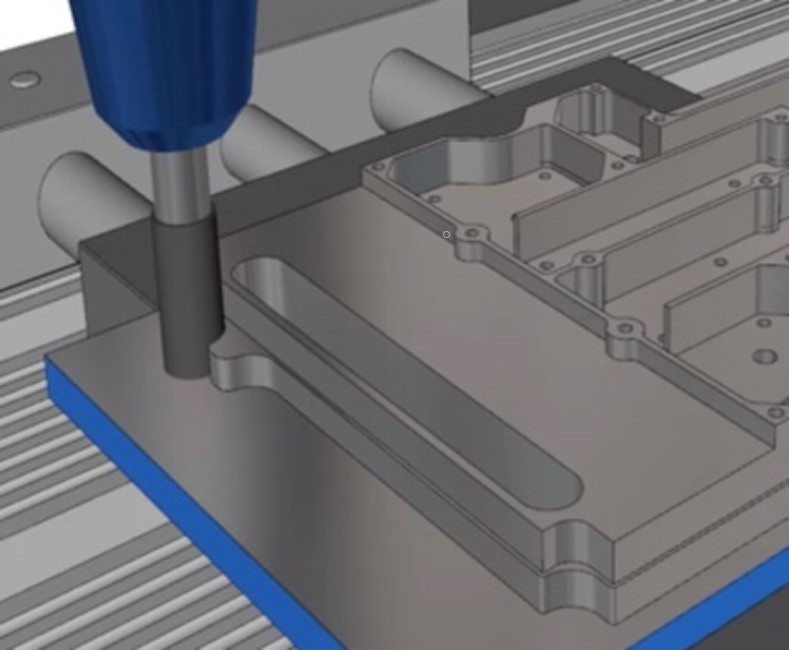
The Role of CNC Machining in Industry 4.0
Explore how CNC machining is being integrated into the Industry 4.0 framework, including topics such as automation, data analytics, connectivity, and smart manufacturing.
> 3-Day Lightning Delivery
> North America’s Top 10 One-stop Solutions
> 75+ Choices of Materials
Industry 4.0, the fourth industrial revolution, is transforming the manufacturing landscape through the integration of advanced technologies and automation. CNC machining, as a cornerstone of modern manufacturing, plays a pivotal role in driving the adoption of Industry 4.0 principles. In this blog, we will explore the significance of CNC machining in the Industry 4.0 framework. We will delve into key areas such as automation, data analytics, connectivity, and smart manufacturing, highlighting how CNC machining is revolutionizing manufacturing processes and paving the way for increased efficiency, productivity, and competitiveness.
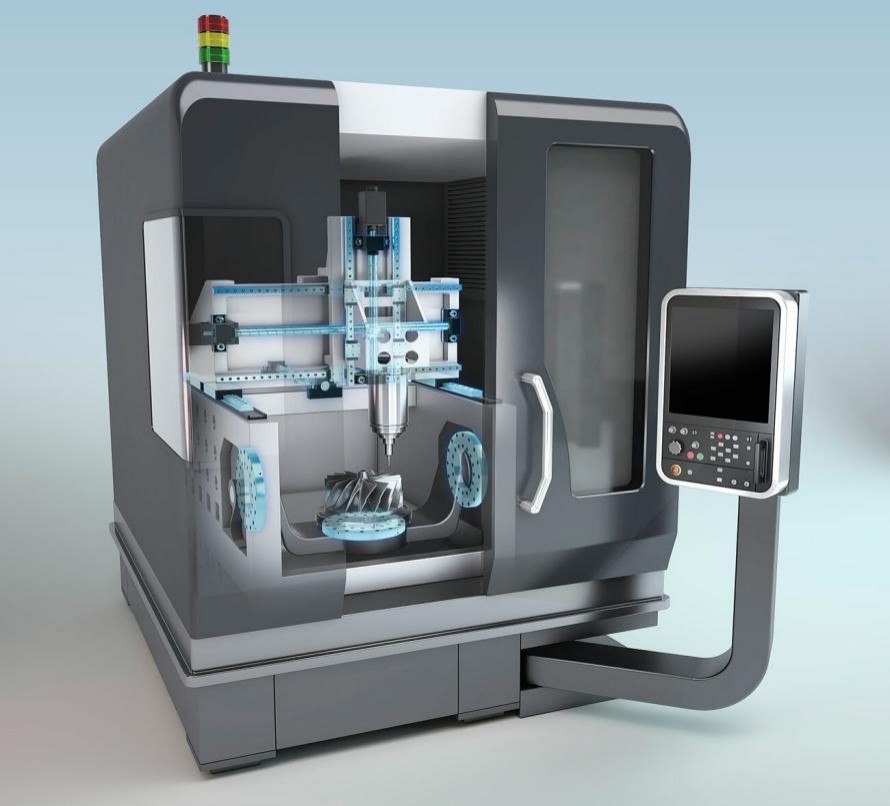
1.Automation in CNC Machining :
Automation is a key element of Industry 4.0, and CNC machining is at the forefront of this revolution. Through the integration of robotics and advanced control systems, CNC machines can operate autonomously, minimizing human intervention and enhancing productivity. We will discuss the benefits of automation in CNC machining, including increased efficiency, reduced labor costs, and improved accuracy. Additionally, we will explore real-world examples of automated CNC machining systems and their impact on manufacturing operations.
2.Data Analytics and CNC Machining :
Data analytics plays a crucial role in Industry 4.0, enabling manufacturers to gather, analyze, and leverage data for informed decision-making. In the context of CNC machining, we will examine how data analytics is transforming the manufacturing process. From real-time monitoring and predictive maintenance to optimization of cutting parameters and tool life, data analytics provides valuable insights that lead to improved efficiency, reduced downtime, and enhanced overall equipment effectiveness (OEE).
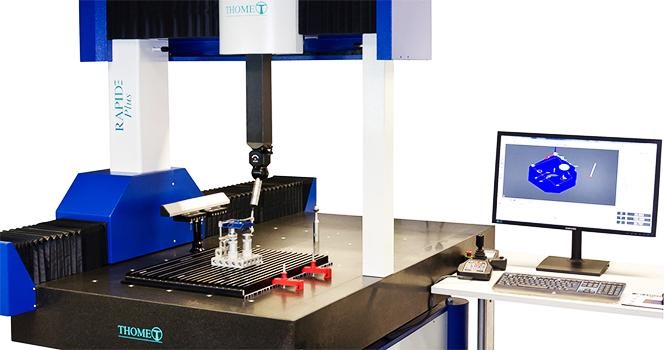
3.Connectivity and CNC Machining :
Connectivity is a fundamental aspect of Industry 4.0, facilitating seamless communication and information exchange between machines, systems, and stakeholders. In the realm of CNC machining, we will explore the concept of the Industrial Internet of Things (IIoT) and how it enables connected CNC machines. We will discuss the benefits of connectivity, such as remote monitoring, centralized control, and real-time data sharing, which empower manufacturers to optimize production processes and make data-driven decisions.
4.Smart Manufacturing and CNC Machining :
Smart manufacturing encompasses the integration of technologies and intelligent systems to create highly efficient and adaptive production environments. We will discuss how CNC machining is an integral part of smart manufacturing, enabling the implementation of advanced features such as adaptive machining, digital twin simulations, and production line optimization. By embracing smart manufacturing principles, manufacturers can achieve increased flexibility, customization, and responsiveness to market demands.
As Industry 4.0 continues to reshape the manufacturing landscape, CNC machining plays a critical role in driving the adoption of advanced technologies and automation. From automation and data analytics to connectivity and smart manufacturing, CNC machining is at the forefront of this revolution, enabling manufacturers to achieve greater efficiency, productivity, and competitiveness. By embracing the principles of Industry 4.0 and leveraging the capabilities of CNC machining, companies can unlock new opportunities for growth and innovation. As we move forward, the integration of CNC machining into the Industry 4.0 framework will continue to revolutionize manufacturing processes and pave the way for a more sustainable and technologically advanced future.