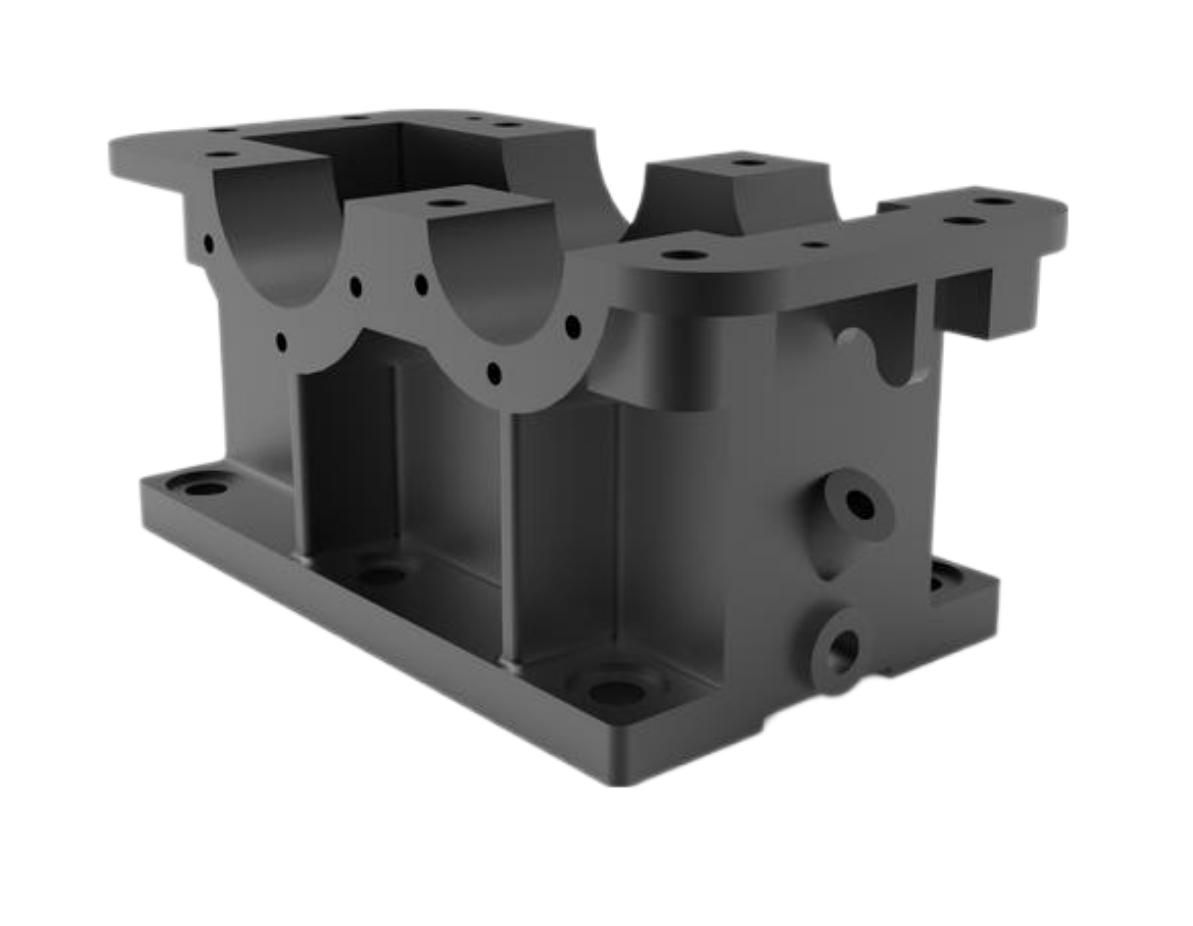
Design Tips of CNC Machining
When designing for CNC machining, consider factors such as part geometry, material selection, toolpath strategy, and surface finish requirements to optimize for accuracy and efficiency.
> 3-Day Lightning Delivery
> North America’s Top 10 One-stop Solutions
> 75+ Choices of Materials
10 Design Tips of CNC Machining
Designing parts for CNC machining requires careful consideration of various factors to ensure optimal functionality, manufacturability, and cost-effectiveness. By following certain design tips, you can enhance the quality, precision, and efficiency of CNC machined parts. Here are some key considerations to keep in mind when designing parts for CNC machining:
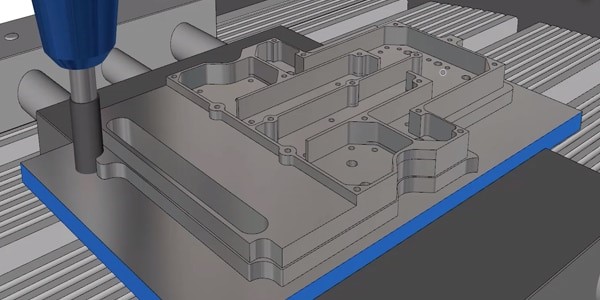
Tip 1: Material Selection
- Choose materials suitable for CNC machining, such as metals (aluminum, steel, titanium) or engineering plastics (ABS, PVC, nylon), based on the specific requirements of your part.
- Consider factors such as mechanical properties, thermal stability, corrosion resistance, and cost when selecting the material.
Tip 2: Design for Manufacturability:
- Simplify the design and avoid complex geometries that can increase machining time and cost.
- Minimize the number of setups and tool changes to improve efficiency.
- Utilize standard tool sizes and shapes whenever possible to avoid custom tooling costs.
- Consider the capabilities and limitations of the CNC machine, including its axis movements, tool access, and spindle speeds.
Tip 3: Dimensional Accuracy and Tolerances:
- Clearly specify critical dimensions and tolerances to ensure proper fit and function of the part.
- Consult with your CNC machining provider to determine achievable tolerances based on the chosen material and machining process.
- Consider the impact of tolerances on the overall cost and functionality of the part.
Tip 4: Wall Thickness:
- Maintain uniform wall thickness throughout the part to prevent issues like warping, distortion, or poor surface finish.
- Avoid sudden changes in wall thickness to ensure consistent machining and structural integrity.
- Design thicker sections to improve strength and rigidity when necessary.
Tip 5: Fillets and Radii:
- Incorporate fillets and radii at sharp corners and edges to improve the part’s strength, reduce stress concentration, and enhance the overall aesthetics.
- Avoid sharp internal corners that can be difficult to machine accurately.
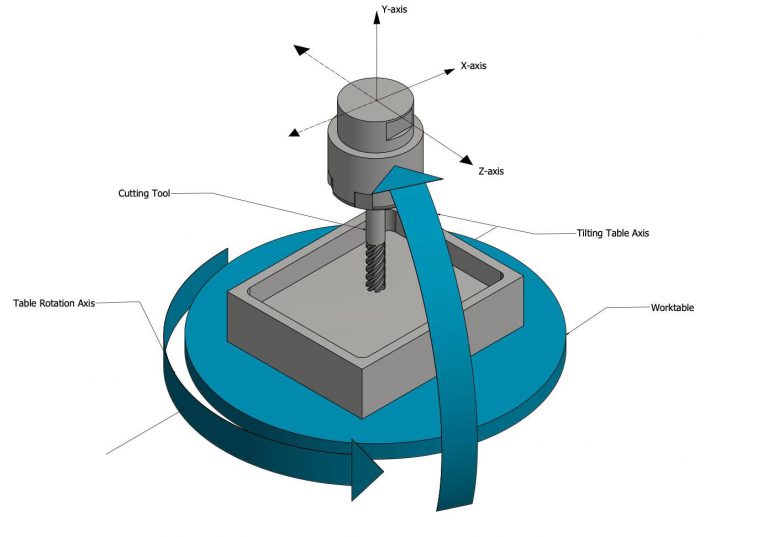
Tip 6: Hole and Slot Sizes
- Design holes and slots with appropriate sizes and tolerances to accommodate fasteners, bearings, or other components.
- Consider the aspect ratio of deep holes to avoid issues with chip evacuation during machining.
- Incorporate chamfers or counterbores for ease of assembly or alignment.
Tip 7: Surface Finish Requirements
- Clearly specify the desired surface finish for critical surfaces and functional areas of the part.
- Consult with your CNC machining provider to determine achievable surface finishes based on the chosen material and machining process.
- Consider the impact of surface finish on part functionality, aesthetics, and post-machining treatments.
Tip 8: Avoid Undercuts
- Minimize or eliminate undercuts in the design as they may require additional machining operations, such as using special tooling or employing secondary processes like EDM (Electrical Discharge Machining).
- If undercuts are necessary, discuss them with your CNC machining provider to explore alternative machining strategies or Post-Processing.
Tip 9: Part Consolidation
- Whenever possible, consolidate multiple parts into a single component to simplify assembly, reduce overall costs, and improve overall part performance.
- Analyze the assembly requirements and identify opportunities for reducing part count without compromising functionality.
Tip 10: Prototype and Test
- Before proceeding with full production, consider prototyping and testing the design to identify and address any potential issues or improvements.
- Rapid prototyping techniques like 3D printing can be used to validate the design before committing to CNC machining.
Looking for CNC Machining Services On-demand?
Are you in need of high-quality CNC Machining services on-demand? Look no further than Naxtry! Our experienced team and state-of-the-art equipment ensure precise and efficient manufacturing of your parts or products. Contact us today for a quote!