
Design Tips of CNC Turning
CNC turning design tips help optimize part production. Experts suggest reducing part complexity, choosing the right material, and selecting the appropriate cutting tools.
> 3-Day Lightning Delivery
> North America’s Top 10 One-stop Solutions
> 75+ Choices of Materials
Design Tips of CNC Turning
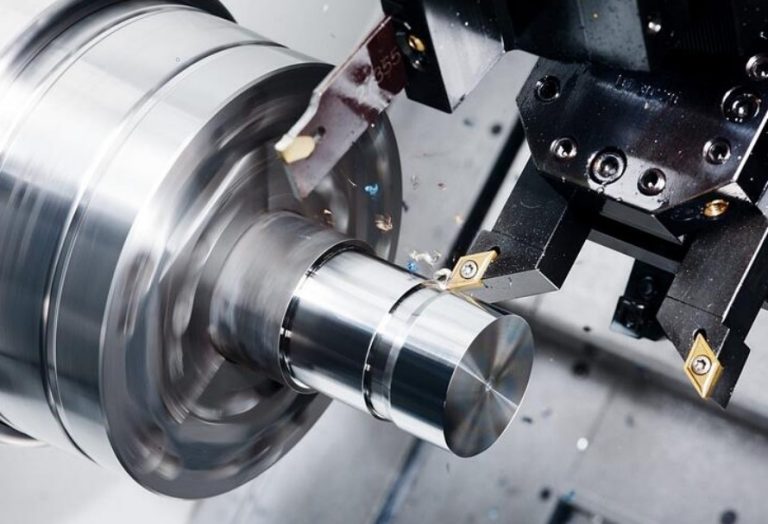
Tip 1: Minimize part length and diameter
One of the main advantages of CNC turning is its ability to create long, thin parts with high precision. However, long, slender parts can be difficult to machine without causing vibration or other machining problems. To minimize these issues, it is important to keep the length and diameter of the part as small as possible. This can help to reduce the cutting forces and improve the rigidity of the workpiece, which can lead to a better surface finish and more accurate dimensions.
Tip 2: Use proper stock material
Choosing the right stock material is critical to the success of any machining process, and CNC turning is no exception. When selecting stock material for CNC turning, it is important to consider the properties of the material, such as its hardness, toughness, and machinability. Materials with high machinability, such as brass or aluminum, are often preferred for CNC turning because they can be machined quickly and efficiently. However, harder materials, such as stainless steel or titanium, may be necessary for certain applications.
Tip 3: Consider tool selection and placement
The selection and placement of cutting tools is another important consideration when designing parts for CNC turning. The cutting tool should be chosen based on the material being machined, the desired surface finish, and the cutting forces required to remove material. The tool should also be placed in a position that allows it to reach all necessary areas of the workpiece without causing interference with other components. In addition, the tool should be oriented in a way that minimizes cutting forces and improves the rigidity of the workpiece.
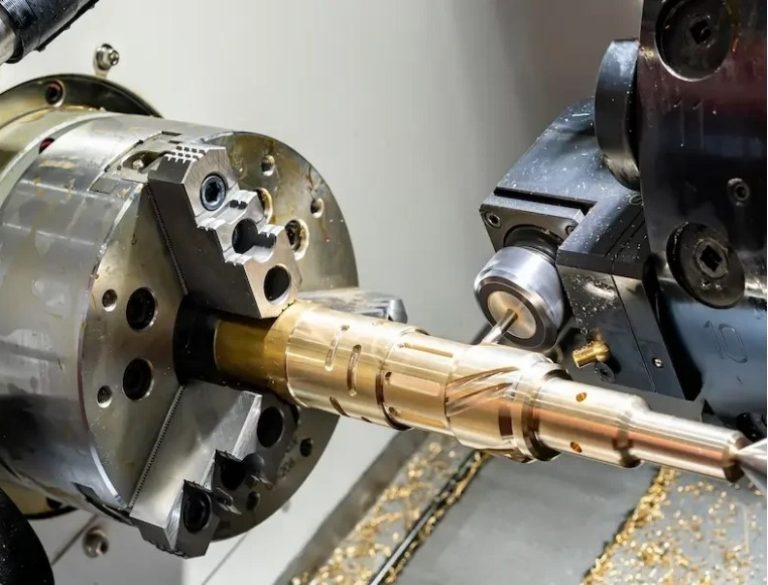
Tip 4: Use proper tolerances
Tolerances are an important consideration in any machining process, and CNC turning is no exception. When designing parts for CNC turning, it is important to consider the tolerance requirements of the application and design the part accordingly. Tighter tolerances can lead to higher precision and accuracy, but can also increase machining time and costs. As a result, it is important to balance the requirements of the application with the cost and time constraints of the machining process.
Tip 5: Minimize tool changes
Tool changes can be time-consuming and can increase the overall cost of the machining process. To minimize tool changes, it is important to design the part so that it can be machined with as few tools as possible. This can be accomplished by using multi-axis machining, which allows for more complex shapes to be machined with a single tool, or by designing the part with simpler features that can be machined using a single tool.
Tip 6: Consider post-machining operations
Post-machining operations, such as heat treatment or surface finishing, can have a significant impact on the final quality of the part. When designing parts for CNC turning, it is important to consider any necessary post-machining operations and design the part accordingly. For example, if a high-quality surface finish is required, the part may need to be designed with a larger diameter to allow for additional material to be removed during finishing.
Looking for CNC Turning Services On-demand?
Are you in need of high-quality CNC Turning services on-demand? Look no further than Naxtry! Our experienced team and state-of-the-art equipment ensure precise and efficient manufacturing of your parts or products. Contact us today for a quote!