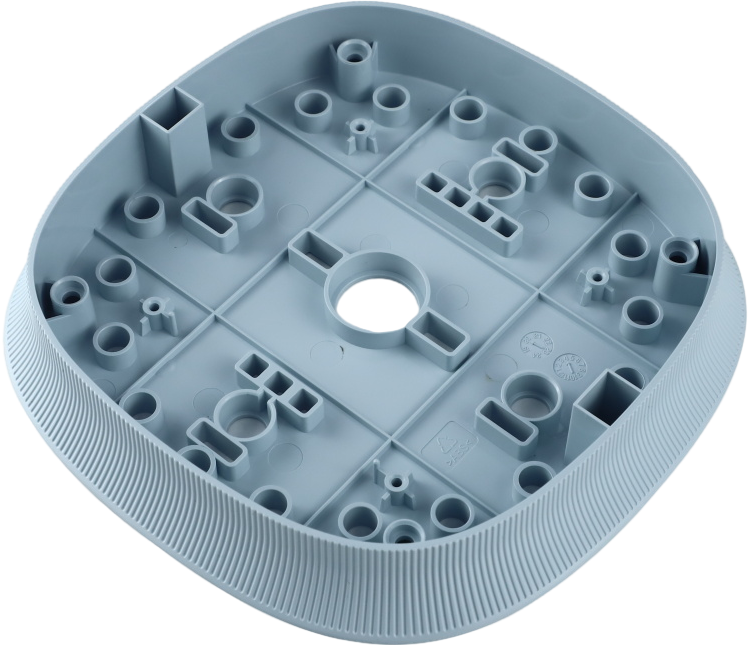
Design Tips of Plastic Injection Molding
Design parts with uniform wall thickness, rounded edges, and draft angles for easy ejection. Use appropriate gate and vent sizes, and avoid sharp corners or undercuts.
> 3-Day Lightning Delivery
> North America’s Top 10 One-stop Solutions
> 75+ Choices of Materials
Design Tips of Plastic Injection Molding
Designing a plastic part for injection molding requires careful consideration of various factors to ensure a successful manufacturing process. Here are 6 design tips to help you create a part that is optimized for plastic injection molding.
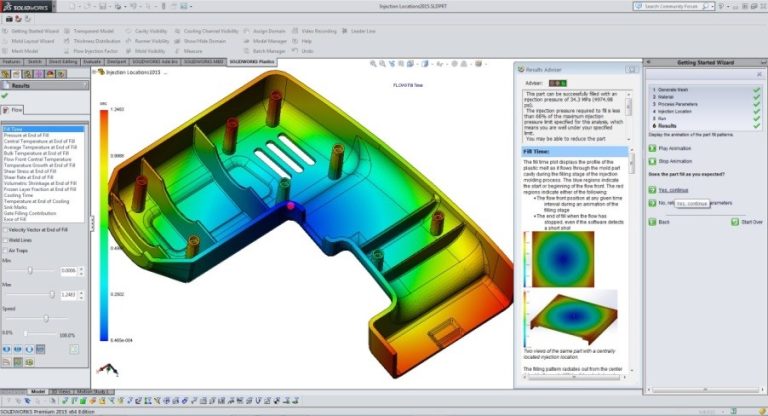
Tip 1: Draft Angles
Draft angles are crucial to successful plastic injection molding. These are tapers or slopes that are added to the walls of the mold to allow for the easy ejection of the part from the mold. The recommended draft angle is typically around 1 to 2 degrees per side, although it can vary depending on the specific material being used. Without sufficient draft angles, the part can become stuck in the mold, leading to manufacturing defects and production delays.
Tip 2: Wall Thickness
Uniform wall thickness is essential for plastic injection molding. Thick sections can lead to cooling issues, resulting in warpage or shrinkage, while thin sections can cause flow imbalances or sink marks. As a general rule of thumb, aim for a wall thickness between 0.040 to 0.160 inches. In cases where thicker walls are required, use a rib structure to maintain rigidity while reducing the overall material usage.
Tip 3: Ribs and Bosses
Ribs are thin, raised sections of material that run perpendicular to the main walls of a part. They help to add rigidity and strength to the part while reducing its overall weight. Bosses are raised features that are used to create mounting points, threaded holes, or other types of attachments. Both ribs and bosses are commonly used in plastic injection molding but require careful design considerations, such as maintaining uniform wall thickness and appropriate draft angles.
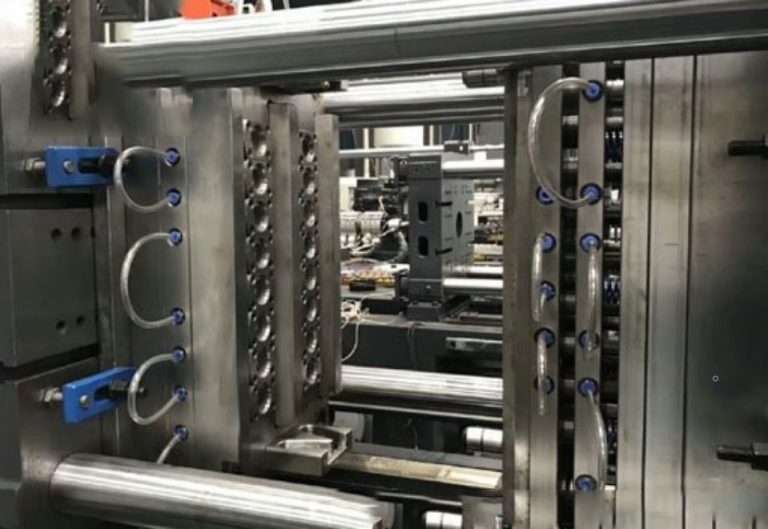
Tip 4: Gate Location
The gate is the point at which molten plastic enters the mold cavity. Its location is critical in determining the overall quality of the part. Gates should be placed in a location that will allow for proper filling of the cavity, minimizing any potential flow imbalances or sink marks. A good rule of thumb is to place the gate at the thickest part of the wall, allowing the plastic to flow more easily into the thinner areas.
Tip 5: Undercuts and Threads
Undercuts and threads are common design features in plastic parts but can pose challenges in injection molding. An undercut is a feature that extends below the parting line of the mold, making it difficult to remove the part from the mold. Threads can be difficult to mold due to their complex geometry. Both features require careful consideration during the design phase to ensure successful manufacturing. Solutions may include the use of sliders, cores, or insert molding.
Tip 6: Material Selection
The choice of material for a plastic part is a crucial consideration in the design phase. Different materials have varying properties, such as flexibility, strength, and resistance to heat or chemicals. It is important to choose a material that is suitable for the intended application and can withstand the manufacturing process without degradation or deformation. It is also important to consider the environmental impact of the material and any regulations or certifications required for its use.