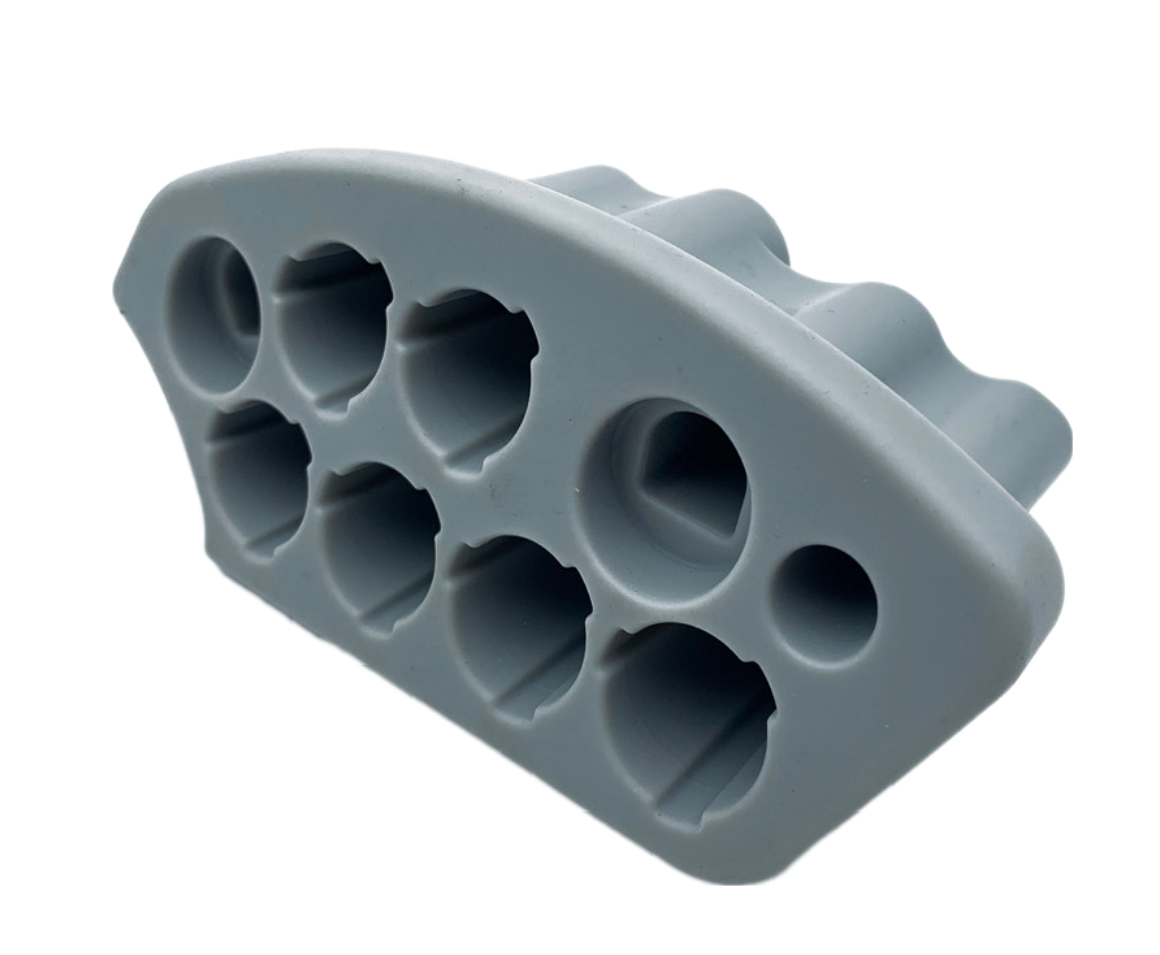
Design Tips of Rubber Molding
When designing for Rubber molding, consider the material's shrinkage rate, mold release, draft angles, and wall thickness to ensure a successful molding process.
> 3-Day Lightning Delivery
> North America’s Top 10 One-stop Solutions
> 75+ Choices of Materials
Design Tips of Rubber Molding
Rubber molding is a manufacturing process that involves molding Rubber into various shapes and sizes. This process is widely used in industries such as automotive, medical, and consumer products. If you are designing a Rubber product, it is important to consider certain design tips to ensure that your product is manufactured effectively and efficiently. Here are six design tips for Rubber molding:
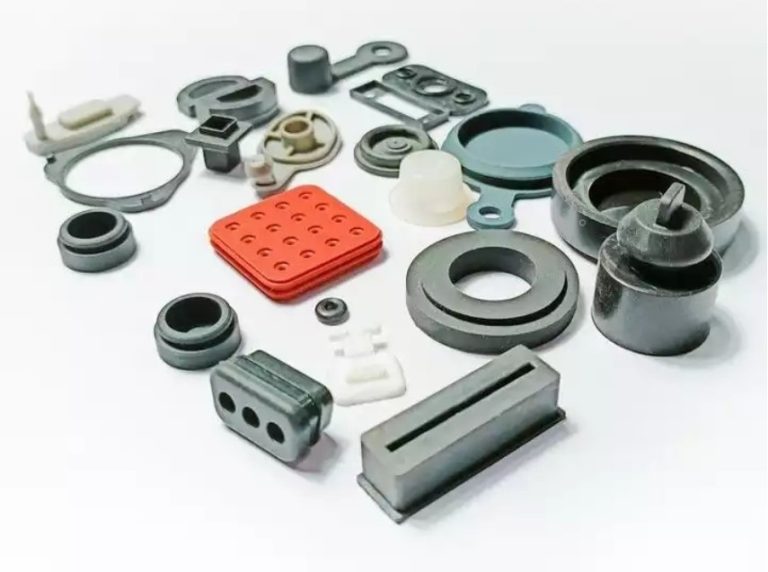
Tip 1: Keep the design simple
One of the most important things to keep in mind when designing for Rubber molding is to keep the design as simple as possible. Complex shapes and features can make the molding process more difficult and can increase the likelihood of defects in the final product. By keeping the design simple, you can reduce the cost and complexity of the molding process.
Tip 2: Use draft angles
Draft angles are essential in Rubber molding as they allow the part to be easily removed from the mold. Draft angles are the angled surfaces on a part that allow it to be released from the mold without damaging the part or the mold. A typical draft angle for Rubber molding is around 1 to 2 degrees.
Tip 3: Design for flash
Flash is the excess material that is produced when Rubber is injected into the mold. Designing your part to accommodate flash is important as it can help to prevent defects in the final product. When designing for flash, you should add extra material to the part to account for the excess material that will be produced during the molding process.
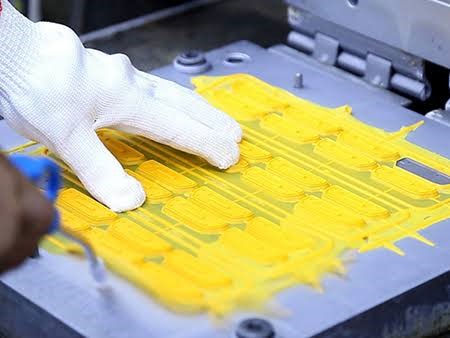
Tip 4: Consider the parting line
The parting line is the line where the two halves of the mold meet. It is important to design your part with the parting line in mind, as this can affect the overall quality of the final product. By designing your part with the parting line in mind, you can ensure that the part is evenly filled and that there are no visible parting lines on the final product.
Tip 5: Choose the right material
There are many different types of Rubber available for molding, each with its own properties and characteristics. When designing for Rubber molding, it is important to choose the right material for your application. Factors to consider include temperature resistance, chemical resistance, and hardness.
Tip 6: Consult with a manufacturer
If you are designing a Rubber product for the first time, it is a good idea to consult with a manufacturer who specializes in Rubber molding. A manufacturer can provide you with valuable insights and recommendations on how to design your part for optimal performance and manufacturing efficiency.