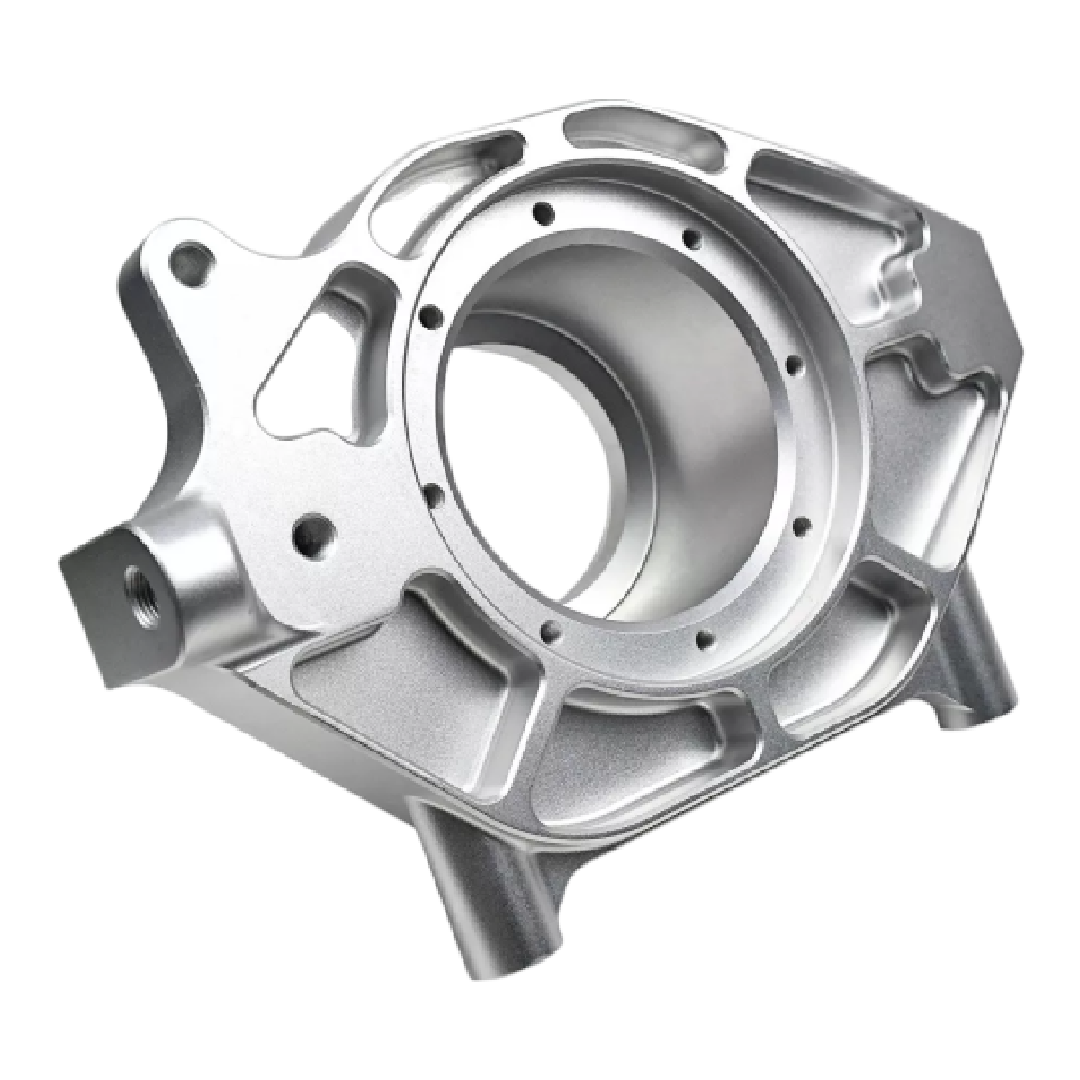
Design Tips of Surface Finishing
Consider the material and application of your product to determine the appropriate surface finishing process, such as powder coating, or anodizing.
> 3-Day Lightning Delivery
> North America’s Top 10 One-stop Solutions
> 75+ Choices of Materials
Design Tips of Surface Finishing
Surface finishing is an important aspect of manufacturing that can greatly impact the final product’s appearance, performance, and durability. There are various techniques used for surface finishing, including polishing, plating, anodizing, painting, and powder coating. In this article, we will discuss six design tips for surface finishing to help you achieve the desired finish for your product.
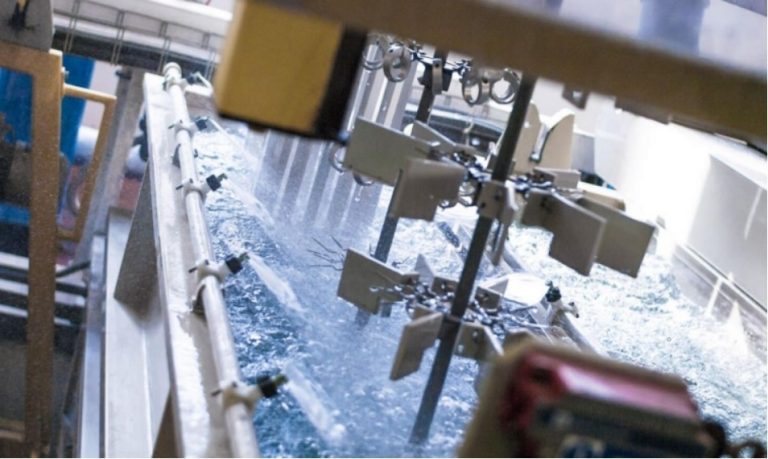
Tip 1: Understand the Material
The first tip for designing for surface finishing is to understand the material you are working with. Different materials react differently to surface finishing techniques. For example, certain materials like aluminum are more susceptible to corrosion and require special surface treatments. Additionally, certain surface finishes may not adhere properly to some materials. By understanding the characteristics of the material, you can choose the right surface finishing technique and ensure that the finish is durable and long-lasting.
Tip 2: Consider the Geometry
The geometry of the part being finished is another important factor to consider. Complex geometries may require specialized techniques or additional steps in the finishing process to achieve the desired result. For example, parts with sharp edges or corners may require additional polishing or deburring to remove any burrs or rough edges. On the other hand, parts with large flat surfaces may require more attention to ensure a consistent finish across the entire surface.
Tip 3: Plan for Pre-Treatment
Pre-treatment is an essential step in surface finishing that prepares the surface for the desired finish. Pre-treatment can include cleaning, degreasing, etching, or other methods to remove impurities, improve adhesion, or modify the surface’s characteristics. Designing for pre-treatment involves ensuring that the part is accessible and that the material can withstand the pre-treatment process without being damaged. Additionally, designing for pre-treatment can reduce the overall processing time and cost.
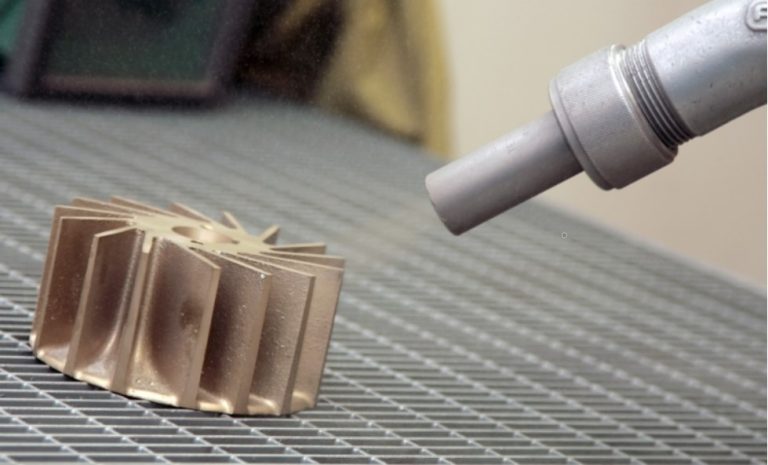
Tip 4: Allow for Tolerance
Surface finishing can affect the final dimensions of the part, particularly when the finish adds a coating or thickness to the surface. It is essential to design for tolerance when considering surface finishing to ensure that the part’s dimensions remain within the required specifications. Tolerances may also need to be adjusted based on the surface finishing technique used, as certain finishes may require additional material to be added to the surface.
Tip 5: Consider the Finish Type
There are various types of surface finishes available, each with unique properties and appearances. Designing for the desired finish type involves understanding the characteristics of each finish and selecting the best fit for the application. For example, some finishes like powder coating or anodizing can provide improved corrosion resistance, while others like polishing or plating can provide a glossy or reflective appearance.
Tip 6: Account for Cost and Lead Time
Finally, designing for surface finishing involves considering the cost and lead time of the finishing process. Some finishing techniques may be more costly or time-consuming than others, and the cost and lead time may vary depending on the part’s complexity or quantity. By designing with cost and lead time in mind, you can ensure that the desired finish is achievable within the required budget and timeline.