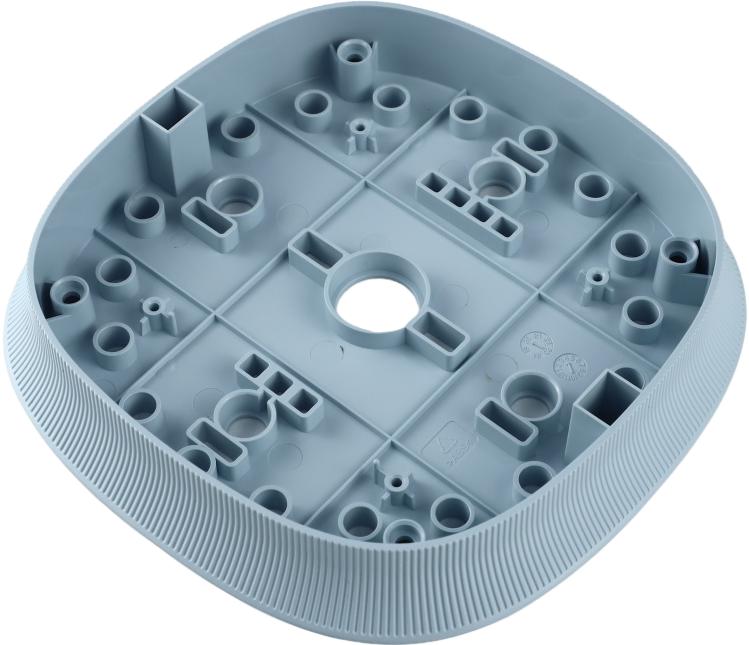
Packaging
Naxtry offers CNC machining, sheet metal fabrication, and injection molding services for the packaging industry. Our services are utilized in crafting a wide range of packaging components, including containers, closures, and specialized packaging solutions.
> 3-Day Lightning Delivery
> North America’s Top 10 One-stop Solutions
> 75+ Choices of Materials
Packaging
The packaging industry demands precision and high-quality components to ensure the safe and efficient containment of products. CNC machining, sheet metal fabrication, and injection molding are crucial manufacturing processes widely employed in the packaging sector to create intricate parts with exact specifications.
CNC Machining in Packaging
CNC machining is a pivotal process in the packaging industry due to its capacity to fabricate top-notch, accurate, and uniform components with precise measurements. This technique entails the utilization of computer-controlled tools to carve and shape a solid material block into a specific form or design. These CNC machining tools are usually constructed from high-speed steel, carbide, or other durable materials, enabling them to effortlessly work with materials like plastics, metals, and composites commonly used in the packaging field.
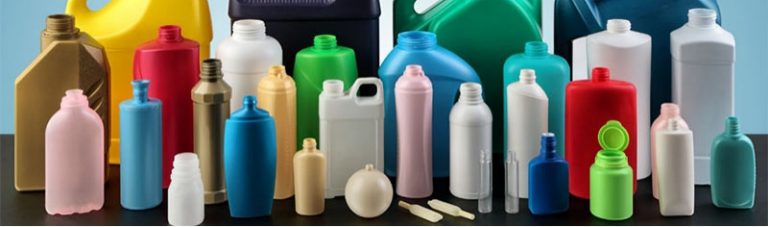
5 Advantages of CNC Machining in Packaging
1.Precision and Accuracy: CNC machining offers unparalleled precision and accuracy. In packaging, where precise fits and tight tolerances are crucial to prevent product damage or contamination, CNC machining ensures that each component meets exact specifications consistently. This precision is vital for creating components like bottle caps, closures, and seals that need to maintain a tight seal to preserve product integrity.
2.Customization: CNC machining allows for extensive customization in packaging design. Whether it’s intricate patterns, unique shapes, or specific sizes, CNC machines can produce packaging components tailored to the exact requirements of a product or brand. This flexibility is especially valuable in the competitive packaging industry, where distinctive designs can set products apart on the shelf.
3.Material Versatility: CNC machines can work with a wide range of materials commonly used in packaging, including plastics, metals, and composites. This versatility allows packaging designers to select materials that align with their product’s needs, whether it’s the lightweight and cost-effective nature of plastics or the durability and aesthetics of metals.
4.Cost-Effective Prototyping: CNC machining is cost-effective for prototyping and small to medium production runs. Unlike traditional manufacturing methods that may require expensive molds or tooling changes, CNC machining eliminates these upfront costs. This makes it an efficient choice for testing and refining packaging designs, reducing time to market, and minimizing expenses associated with design iterations.
5.Efficiency and Speed: CNC machines are known for their efficiency and speed. In the fast-paced packaging industry, where responsiveness to market demands is essential, CNC machining ensures that components can be produced quickly and accurately. This capability enables packaging manufacturers to meet tight production schedules and respond promptly to changes in packaging requirements, such as adjustments due to market trends or regulatory updates.
These advantages collectively make CNC machining a valuable and versatile tool in the packaging industry, allowing companies to create high-quality, customized, and cost-effective packaging solutions that meet the evolving needs of their products and customers.
Sheet Metal Fabrication in Packaging
Sheet metal fabrication plays a significant role in the packaging industry, contributing to the creation of various components and solutions. Here’s how sheet metal fabrication is utilized in packaging:
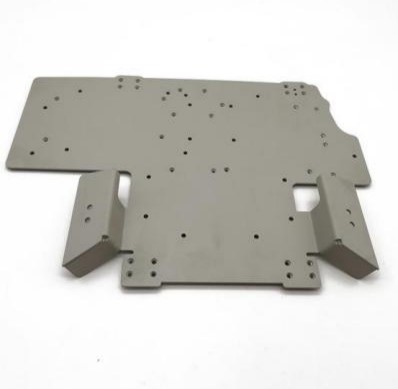
1.Custom Packaging Solutions: Sheet metal fabrication enables the design and production of custom packaging solutions tailored to specific products or industries. Whether it’s metal enclosures for electronic components, specialized brackets for securing items within packaging, or unique containers, sheet metal can be shaped to fit precise requirements.
2.Durable and Protective Packaging: Metal is known for its durability and strength. In packaging, it’s often used to create protective casings, containers, or enclosures that safeguard products during transit and storage. These metal components can withstand harsh handling, impacts, and environmental factors.
3.Aesthetic Packaging: Sheet metal can be formed into aesthetically pleasing packaging designs. This is particularly valuable for premium and luxury products, where the packaging itself is a part of the brand’s image. Metal packaging can be intricately detailed, embossed, or finished with various coatings to create a visually appealing presentation.
4.Secure Closures: Metal closures, such as caps and lids, are common in the packaging of beverages, cosmetics, and other products. These closures provide a secure seal that prevents leakage and maintains product freshness. Sheet metal fabrication ensures the precise manufacturing of these closures to meet industry standards.
5.Environmental Sustainability: Sheet metal is a recyclable material, contributing to sustainability efforts in packaging. Many industries are adopting eco-friendly packaging solutions, and using sheet metal that can be recycled aligns with these environmental goals.
6.High-Volume Production: Sheet metal fabrication processes can handle high-volume production runs efficiently. This scalability is crucial for industries where large quantities of packaging components are required, such as food and beverage manufacturing or electronics.
7.Cost-Effective Solutions: Despite the initial tooling and setup costs, sheet metal fabrication often proves cost-effective for bulk production due to its durability and longevity. It can reduce long-term packaging costs by providing robust and reusable solutions.
8.Variety of Materials: Sheet metal fabrication allows for the use of different types of metals, including steel, aluminum, and stainless steel. This versatility in materials enables packaging designers to select the metal that best suits the product’s requirements in terms of weight, strength, and corrosion resistance.
Injection Molding in Packaging
Injection molding is a highly versatile manufacturing process that plays a pivotal role in the packaging industry. Here’s how injection molding is utilized in packaging:
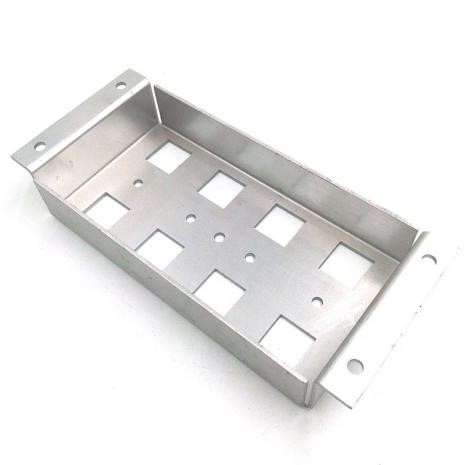
1.Custom Packaging Design: Injection molding allows for the creation of highly customized packaging components. Designers can create intricate shapes, unique closures, and specialized features to meet the specific requirements of products or brands. This flexibility is especially beneficial for companies looking to distinguish their products on store shelves.
2.High-Quality Finish: Injection molding can produce packaging components with a high-quality finish. This is crucial for packaging in industries like cosmetics or luxury goods, where aesthetics and presentation are paramount. Injection-molded components can be designed with smooth surfaces and intricate details, enhancing the overall visual appeal.
3.Consistency and Precision: Injection molding ensures consistent and precise production of packaging components. Each part is identical, meeting tight tolerances and quality standards. This uniformity is critical in packaging to ensure that closures, seals, and other components function as intended.
4.Efficiency in Mass Production: Injection molding is well-suited for mass production of packaging components. It can produce large quantities of identical parts quickly and cost-effectively. This efficiency is crucial for industries where high volumes of packaging are required, such as food and beverage or consumer goods.
5.Diverse Material Options: Injection molding supports a wide range of materials, including various plastics and elastomers. Packaging designers can choose materials that align with product requirements, such as flexibility, durability, or resistance to chemicals or UV radiation.
6.Complex Shapes and Features: Injection molding can create packaging components with complex shapes and integrated features. This capability is essential for designing packaging solutions that are not only functional but also innovative. For example, caps with tamper-evident features or handles for ease of carrying.
7.Cost-Effective Tooling: While the initial tooling costs for injection molding can be significant, they are often offset by the cost-effectiveness of mass production. Once the molds are created, they can be used repeatedly, reducing per-unit production costs over time.
8.Sustainability: Many injection-molded materials are recyclable, contributing to sustainability efforts in packaging. Companies can choose recyclable materials to align with environmental goals.
9.Product Protection: Injection-molded packaging components, such as caps, seals, and containers, play a critical role in protecting products from contamination, leakage, and environmental factors.
In summary, injection molding is a versatile and efficient manufacturing process used extensively in the packaging industry. It enables the production of high-quality, customized, and cost-effective packaging solutions, making it a valuable tool for packaging designers and manufacturers.
Our On-Demand Manufacturing Services
Naxtry’s factory offers a one-stop solution for CNC machining, sheet metal fabrication, and injection molding services, providing high-quality products to various industries.
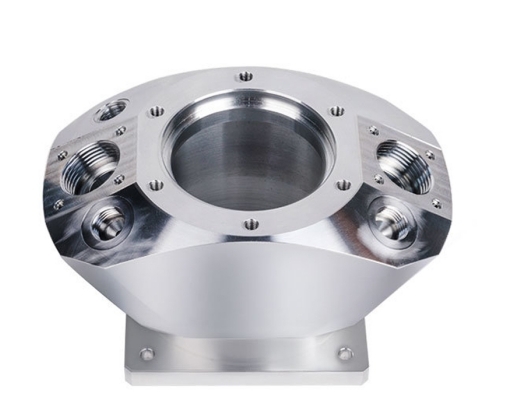
Sheet Metal Fabrication
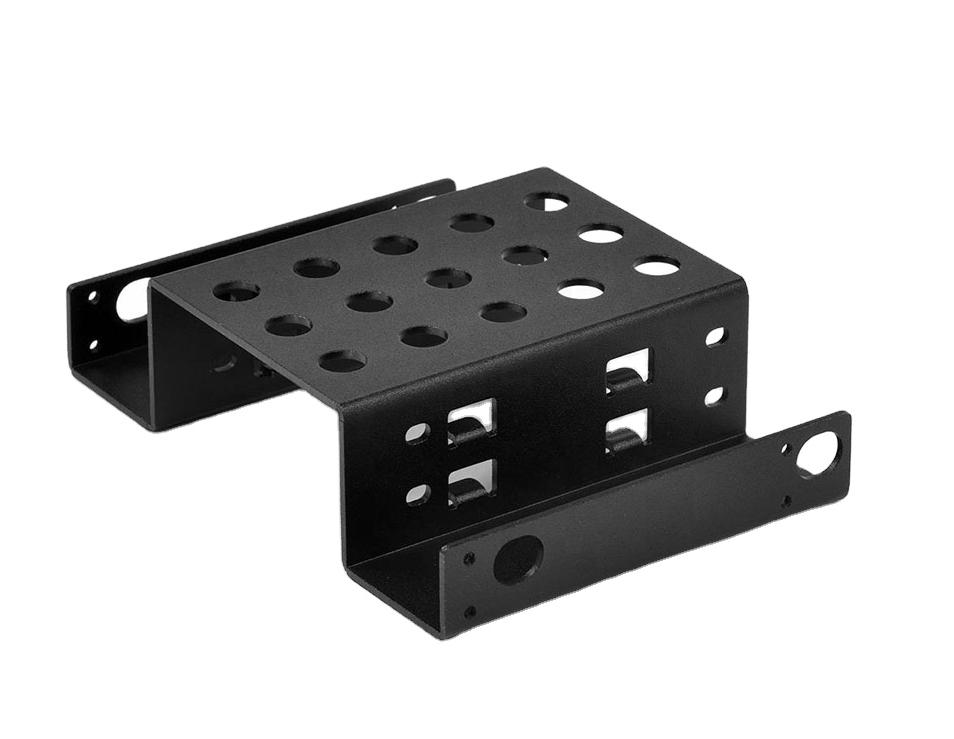
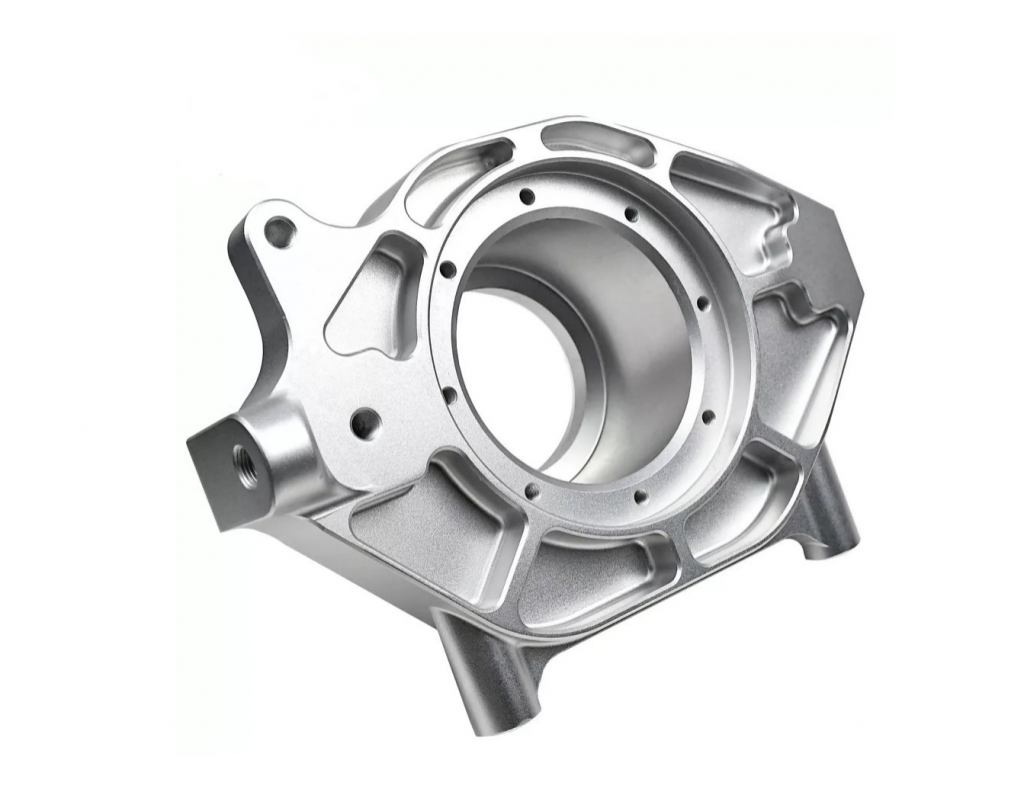